Guidelines for having the right workplace facilities
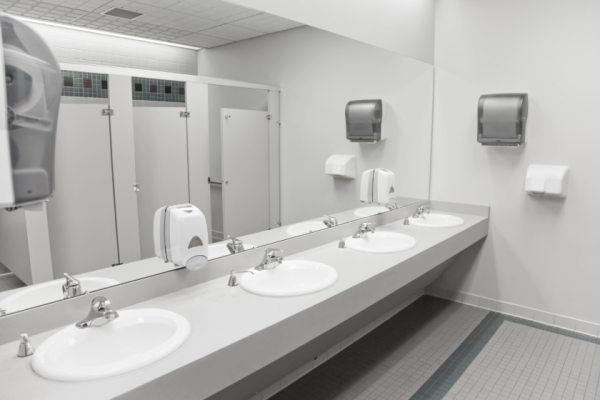
Guidelines for having the right workplace facilities
Employers must provide welfare facilities and a working environment that's healthy and safe for everyone in the workplace, including those with disabilities.
You must have:
- Welfare facilities – the right number of toilets and washbasins, drinking water and having somewhere to rest and eat meals.
- A healthy working environment – a clean workplace with a reasonable working temperature, good ventilation, suitable lighting and the right amount of space and seating
- A safe workplace – well-maintained equipment, with no obstructions in floors and traffic routes, and windows that can be easily opened and cleaned.
What you must provide for a safe and healthy workplace:
Welfare facilities
Workers must have access to:
- Toilets and hand basins, with soap and towels or a hand dryer
- Drinking water
- A place to store clothing (and somewhere to change if special clothing is worn for work)
- somewhere to rest and eat meals.
A healthy working environment
To have a healthy working environment, make sure there is:
- Good ventilation – a supply of fresh, clean air drawn from outside or a ventilation system.
- A reasonable working temperature so it's comfortable to work (usually at least 16°C, or 13°C for strenuous work, unless other laws require lower temperatures)
- Lighting suitable for the work being carried out.
- Enough room space and suitable workstations and seating
- A clean workplace with appropriate waste containers
A safe workplace
To keep your workplace safe, you must:
- Maintain your premises and work equipment.
- Keep floors and traffic routes free of obstructions.
- Have windows that can be opened and cleaned safely.
- Make sure that any transparent (eg glass) doors or walls are protected or made of safety material
Weekly testing of fire alarms
To meet the legal requirements of BS5839, weekly testing of fire alarms in commercial properties or those with multiple occupancy such as flats and apartment blocks is mandatory. Each and every week, a manual test on all fire alarms must be carried out during normal working hours to test that everything is in working order. This is to check that the system itself is capable of alerting and alarming sufficiently and that any fire alarm signal is correctly received at any alarm-receiving centre.
Legionella
Legionella control is crucial because Legionella bacteria can cause Legionnaires' disease, a potentially fatal form of pneumonia. The bacteria are commonly found in aquatic environments and can proliferate in purpose-built water systems such as cooling towers, hot and cold water systems if conditions are favourable. These systems can become a source of infection if not properly managed, leading to outbreaks of Legionnaires' disease. The bacteria multiply in water temperatures between 20°C and 45°C, and can grow in biofilms, sludge, scale, and areas of stagnation. When contaminated water droplets or aerosols are inhaled, they can cause infection in susceptible individuals.
Companies should prioritise legionella control because it's a matter of public health and safety and it is also a legal requirement. Employers and those in control of premises have a legal duty to ensure the health and safety of their employees and others who may be affected by their work activities. This includes identifying and assessing the risks of Legionella bacteria in their water systems and implementing appropriate control measures. Failing to do so can result in prosecution, even if no cases of Legionnaires' disease occur. Additionally, a responsible approach to legionella control protects the company's reputation and reduces the risk of costly legal battles.
Legionella control is a legal requirement in the UK under the Health and Safety at Work Act 1974 (HSWA), the Control of Substances Hazardous to Health Regulations 2002 (COSHH), and the Management of Health and Safety at Work Regulations 1999. The Health and Safety Executive (HSE) provides guidance through the Approved Code of Practice (ACoP) L8, which outlines the steps that duty holders should take to comply with their legal obligations. The guidance is further supported by technical guidance documents HSG274 Parts 1, 2, and 3, which cover evaporative cooling systems, hot and cold-water systems, and other risk systems. Companies must implement measures to prevent or control the risk of exposure, maintain records, and ensure that a competent person takes responsibility for legionella control.
EICR Fixed Wire Testing
Most standard workplace environments need an Electrical Installation Condition Report to be produced at least every 5 years. However, there should be regular routine inspections conducted at least annually.
Typical workplaces which require 5 Yearly Fixed Wire Testing include:
- Commercial spaces such as offices and retail outlets
- Hotels and restaurants (excluding spa hotels)
- Schools, colleges and universities
- Laboratories
- Community centres, churches and public houses
- Care homes and hospitals (excluding medical locations)
- Halls of residence, houses of multiple occupancy
PAT Testing
There is currently no legal requirement to PAT test, but employers are legally required to create a safe working environment and PAT testing is a great risk management strategy.
Offices, Shops and Hotels – Class 1 equipment including stationery and IT equipment should be tested every 48 months. Moveable equipment such as extension leads, and portable equipment should be tested every 24 months. Handheld equipment should be tested every 12 months.
Public Use Equipment – Stationery and IT equipment such as computers should be tested every 12 months. Moveable, Portable and Handheld equipment falling into Class 2 should be tested every 12 months. Moveable, Portable and Handheld equipment falling into Class 1 should be tested every 6 months.